Министерство образования и науки Российской Федерации
Федеральное государственное бюджетное образовательное учреждение высшего профессионального образования
"УФИМСКИЙ ГОСУДАРСТВЕННЫЙ АВИАЦИОННЫЙ ТЕХНИЧЕСКИЙ УНИВЕРСИТЕТ"
филиал в г.Туймазы
Кафедра «Общеобразовательных дисциплин»
Историко-исследовательская работа
на тему:
«Как и где в самолетостроении впервые появились
композиционные материалы? Их достоинства и недостатки»
Выполнил: студент 1 курса
группы МАТ 104-д
Шаймуратова Д.Р.
Руководитель: доц., канд.хим.наук
Тимербаева Г.Р.
г. Туймазы 2014.
Оглавление
Введение.
Понятие композиционных материалов. Их классификация.
Виды композиционных материалов, используемых в авиастроении.
Получение и применение композиционных материалов в авиастроении
(с момента создания и до наших дней) .
Трудности создания композиционных материалов.
Заключение.
Список литературы.
«Все, что можно представить, - можно осуществить!»
Уильям Клемент Стоун
Введение
Решение всей совокупности сложных конструкционных, схемотехнических и технологических задач при разработке, создании и эксплуатации ракетно-космических и авиационных средств невозможно без широкого развития и внедрения результатов авиакосмического материаловедения. При разработке ракетно-космических и авиационных средств требуются новые материалы, которые должны выдерживать нагрузки полетов (высокие температура и давление, вибрационные нагрузки на этапе выведения, низкие температуры космического пространства, глубокий вакуум, радиационное воздействие, микрочастицы и т.д.) и иметь достаточно низкую удельную массу. Весь спектр сильных, зачастую с резкими переходами воздействий на металлические и неметаллические конструкции и элементы оказывает существенное влияние на их глубинные структурные свойства и, как следствие, на надежность и долговечность авиакосмических средств различного назначения.
Появление композитных материалов на основе углеродного волокна в авиастроении совершило революцию. Еще в 60-е годы авиаконструкторы искали материалы альтернативные тяжеловесным металлам. Предпочтение было отдано легким и прочным композитам. Кроме того, вес композитных деталей составляет не больше 20% аналогичных деталей из алюминия, при превосходящей прочности, гибкости и устойчивости к давлению, не говоря уже о том, что как неметаллы, они, естественно, могут не бояться коррозии.
Область применения композиционных материалов в авиастроении весьма обширна. Они применяются для высоконагруженных деталей самолетов (обшивки, лонжеронов, нервюр, панелей и т. д.) и двигателей (лопатки вентиляторов и компрессоры.), в космической технике для узлов силовых конструкций аппаратов, подвергающихся нагреву, для элементов жесткости, панелей.
Применение композиционных материалов обеспечивает новый качественный скачок в увеличении мощности двигателей, энергетических и транспортных установок, уменьшении массы машин и приборов. Однако, несмотря на все положительные стороны качественных характеристик композиционных материалов, вероятно, существует и обратная сторона медали.
На мой взгляд, композиционные материалы хотя и привносят в авиацию много полезного, однако имеют достаточно большое количество недостатков, которые сдерживают их распространение. Выдвинутая мной гипотеза натолкнула меня на детальное изучение научных изысканий в области создания и применения композитов, а также тщательное изучение характеристик данных материалов.
Понятие композиционных материалов.
Их классификация.

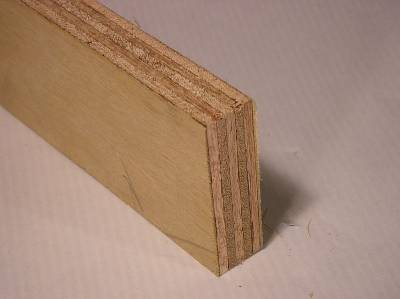
Так что же собой представляет композиционный материал? Итак, в переводе с английского термин "композит" означает сложный. Композиционный материал или композит, — искусственно созданный неоднородный сплошной материал, состоящий из двух или более компонентов с четкой границей раздела между ними. Композиционный материал состоит из высокопрочного наполнителя, ориентированного в определенном направлении, и матрицы. Механическое поведение композиции определяется соотношением свойств армирующих элементов и матрицы, а также прочностью связи между ними. Эффективность и работоспособность материала зависят от правильного выбора исходных компонентов и технологии их совмещения, призванной обеспечить прочную связь между компонентами при сохранении их первоначальных характеристик.
Для создания композиции используются самые разные армирующие наполнители и матрицы. В качестве армирующих наполнителей (силовая основа композиции) применяются волокна бериллия, стекла, графита, стали, карбида кремния, бора или так называемые нитевидные кристаллы окиси алюминия, карбида бора, графита, железа и т. д. Матрицы изготовляются из синтетических смол (эпоксидных, полиэфирных, кремниево-органических) или сплавов металлов (алюминия, титана и других). Соединение волокон или нитевидных кристаллов с матрицей производится горячим прессованием, литьем, плазменным напылением и некоторыми другими способами. В композитах конструкционного назначения армирующие элементы обычно обеспечивают необходимые механические характеристики материала (прочность, жесткость и т.д.), а матрица (или связующее) обеспечивает совместную работу армирующих элементов и защиту их от механических повреждений и агрессивной химической среды.
Центральная идея полимерных композиционных материалов – соединение нескольких компонентов с целью получения материала, который будет обладать свойствами, не присущими этим компонентам по отдельности. По сравнению с традиционными конструкционными материалами полимерные композиционные материалы обладают уникальными физическими, химическими и механическими свойствами и способностью к направленному их изменению в соответствии с назначением создаваемой конструкции.
Патент на создание первых композитов принадлежит великому творцу-природе.Это дерево.
Композиционные материалы по химическому составу делятся на металлические и неметаллические.
1. Композиционные материалы с металлической матрицей.
Композитные материалы или композиционные материалы состоят из металлической матрицы (чаще Al, Mg, Ni и их сплавы), упрочненной высокопрочными волокнами (волокнистые материалы) или тонкодисперсными тугоплавкими частицами, не растворяющимися в основном металле (дисперсно-упрочненные материалы). Металлическая матрица связывает волокна (дисперсные частицы) в единое целое. Волокно (дисперсные частицы) плюс связка (матрица), составляющие ту или иную композицию, получили название композиционные материалы.
2. Композиционные материалы с неметаллической матрицей.
Композиционные материалы с неметаллической матрицей нашли широкое применение. В качестве неметаллических матриц используют полимерные, углеродные и керамические материалы. Из полимерных матриц наибольшее распространение получили эпоксидная, фенолоформальдегидная и полиамидная.
Угольные матрицы коксованные или пироуглеродные получают из синтетических полимеров, подвергнутых пиролизу. Матрица связывает композицию, придавая ей форму. Упрочнителями служат волокна: стеклянные,
углеродные, борные, органические, на основе нитевидных кристаллов (оксидов, карбидов, боридов, нитридов и других), а также металлические (проволоки), обладающие высокой прочностью и жесткостью.
Свойства композиционных материалов зависят от состава компонентов, их сочетания, количественного соотношения и прочности связи между ними. Армирующие материалы могут быть в виде волокон, жгутов, нитей, лент, многослойных тканей.
Часто композиционный материал представляет собой слоистую структуру, в которой каждый слой армирован большим числом параллельных непрерывных волокон. Каждый слой можно армировать также непрерывными волокнами, сотканными в ткань, которая представляет собой исходную форму, по ширине и длине соответствующую конечному материалу. Нередко волокна сплетают в трехмерные структуры.
Композитные материалы отличаются от обычных сплавов более высокими значениями временного сопротивления и предела выносливости (на 50– 10 %), модуля упругости, коэффициента жесткости и пониженной склонностью к трещинообразованию. Применение композиционных материалов повышает жесткость конструкции при одновременном снижении ее металлоемкости.
Прочность композиционных (волокнистых) материалов определяется свойствами волокон; матрица в основном должна перераспределять напряжения между армирующими элементами. Поэтому прочность и модуль упругости волокон должны быть значительно больше, чем прочность и модуль упругости матрицы.
Жесткие армирующие волокна воспринимают напряжения, возникающие в композиции при нагружении, придают ей прочность и жесткость в направлении ориентации волокон.
Для упрочнения алюминия, магния и их сплавов применяют борные, а также волокна из тугоплавких соединений (карбидов, нитридов, боридов и оксидов), имеющих высокие прочность и модуль упругости. Нередко используют в качестве волокон проволоку из высокопрочных сталей.
Для армирования титана и его сплавов применяют молибденовую проволоку, волокна сапфира, карбида кремния и борида титана.
Повышение жаропрочности никелевых сплавов достигается армированием их вольфрамовой или молибденовой проволокой. Металлические волокна используют и в тех случаях, когда требуются высокие теплопроводность и электропроводимость. Перспективными упрочнителями для высокопрочных и высокомодульных волокнистых композиционных материалов являются нитевидные кристаллы из оксида и нитрида алюминия, карбида и нитрида кремния, карбидабора и др.
Композиционные материалы на металлической основе обладают высокой прочностью и жаропрочностью, в то же время они малопластичны. Однако волокна в композиционных материалах уменьшают скорость распространения трещин, зарождающихся в матрице, и практически полностью исчезает внезапное хрупкое разрушение. Отличительной особенностью волокнистых одноосных композиционных материалов являются анизотропия механических свойств вдоль и поперек волокон и малая чувствительность к концентраторам напряжения.
Анизотропия свойств волокнистых композиционных материалов учитывается при конструировании деталей для оптимизации свойств путем согласования поля сопротивления с полями напряжения.
Армирование алюминиевых, магниевых и титановых сплавов непрерывными тугоплавкими волокнами бора, карбида кремния, доборида титана и оксида алюминия значительно повышает жаропрочность. Особенностью композиционных материалов является малая скорость разупрочнения во времени с повышением температуры.
Основным недостатком композиционных материалов с одно и двумерным армированием является низкое сопротивление межслойному сдвигу и поперечному обрыву. Этого лишены материалы с объемным армированием.
Таким образом, волокнистые композиты армированы волокнами или нитевидными кристаллами – кирпичи с соломой и папье-маше можно отнести как раз к этому классу композитов. Уже небольшое содержание наполнителя в композитах такого типа приводит к появлению качественно новых механических свойств материала. Широко варьировать свойства материала позволяет также изменение ориентации размера и концентрации волокон. Кроме того, армирование волокнами придает материалу анизотропию свойств (различие свойств в разных направлениях), а за счет добавки волокон проводников можно придать материалу электропроводность вдоль заданной оси.
На сегодняшний момент активно разрабатываются композиционные материалы нового поколения – так называемые интеллектуальные материалы. Данные композиты способны контролировать напряженно-деформированное состояние в условиях воздействия внешних факторов (нагрузок, температур) и адаптироваться (приспосабливаться) к этим воздействиям, например, путем управления формой для снижения возникающих в нем напряжений. Такие материалы могут применяться для особо ответственных высоконагруженных конструкций. Для осуществления этих функций в структуру материала встраиваются сенсоры – тензорезисторные, оптоволоконные, пьезоэлектрические, которыми могут служить, в том числе армирующие элементы, входящие в состав композиционного материала.
Виды композиционных материалов, используемых в авиастроении.
Стекловолокно - один из самых распространенный армирующих материалов. В процессе его производства возможно получать волокна с физическими свойствами варьирующимися в широком диапазоне. Наиболее широкое применение нашел тип стекловолокна E-glass, благодаря наилучшим физическим качествам при низкой стоимости. Другой тип стекловолокна, S-glass, на 30% прочнее предыдущего, но мало используется в самолетостроении в связи с высокой стоимостью.
Карбоновое волокно или графит представляет собой очень прочный армирующий материал. Он используется в конструкциях лодок, клюшек для гольфа и т.д. Углеволокно сочетает в себе такие качества как низкий удельный вес, прочность и твердость. В индивидуальном самолетостроении углепластик используют в очень ответственных деталях.
Кевлар – это продукт корпорации DuPont. Это один из самых прочных материалов в мире, его используют в изготовлении бронежилетов. Кевлар незаменим для производства деталей, которые при дальнейшей эксплуатации будут подвергать воздействию абразивов. Однако область его применения ограничивается трудностями в обработке и относительно низкой прочности сжатия.
В связи с использованием графито-эпоксидных и стеклопластиковых композитов возникла потребность в разработке неразрушающих методов контроля их прочностных характеристик. Теоретические методы расчета матрицы жесткости композитов из анализа микроструктуры их компонент являются очень сложными и громоздкими, и в большинстве случаев не дают информацию о прочности конструкции. Поэтому для описания упругих свойств композитов обычно вводят усредненные макроскопические характеристики - упругие модули.
На А-380 композиты составят 18 % от веса самолета, главным образом это углеродное волокно или фиброкарбон. В середине 2003 г. фирма Airbus Industries показала фотографии центроплана крыла - основной силовой конструкции большого самолета A380, выполненного из углепластика. И уже через несколько месяцев фирма Boeing объявила о создании нового пассажирского самолета 7Е7 полностью из композиционных материалов. Дальше пошла фирма Bombardier, которая заявила, что ее региональные самолеты и самолеты "бизнес-класса" будут строится по технологиям фирмы Boeing, т.е. станут полностью композитными.
Россия имеет приоритет в изготовлении волокон и нитей из базальта, которые превосходят стеклянные по теплопроводности и жаропрочности в 1,5 раза, по прочности - в 2 раза, по гигроскопичности - в 40 раз. Разрушающие напряжения при растяжении базальтового волокна достигают 480 МПа (у стальной проволоки - 280-350 МПа). ПКМ на основе базальтовых волокон и нитей можно использовать при температурах от -269 до +1000°С.
По физико-химическим свойствам изделия из композиционных материалов на основе базальта превосходят сталь, асбест и другие традиционные материалы в несколько раз, экологически безопасны, а по химической устойчивости относятся к первой категории. Устойчивы к агрессивным средам и в несколько раз долговечнее арматуры из металла.
Использование композитов дает возможность изготавливать довольно крупные элементы планера, сократить трудоемкость производства и за счет уменьшения клепок и соединений снизить его стоимость.
Сегодня полимерные композитные материалы начинают активно применяться в мировом авиастроении. Композиты используют в изготовлении ряда частей авиалайнера. В их числе воздушные тормоза; интерцепторы; элероны; закрылки; рули направления; элемент конструкции сложного закрылка; пилоны; панели коробки приводов; люки коробки приводов; лопасти винтов; панели крыльев вертикального и горизонтального оперения; элементы силового набора (центроплан, кессон, лонжероны, стрингеры, нервюры); элементы обшивки фюзеляжа; элементы внутреннего силового набора (балки и панели полов, перегородки); детали интерьеров и отделки.
Комбинируя объемное содержание компонентов, можно, в зависимости от назначения, получать композиционные материалы с требуемыми значениями прочности, жаропрочности, модуля упругости, абразивной стойкости, а также создавать композиционные материалы с необходимыми магнитными, диэлектрическими, радиопоглощающими и другими специальными свойствами.
Однако механика деформирования и разрушения композитов и конструкций из них не может считаться завершенной. Уже при относительно невысоких значениях эксплуатационных нагрузок в некоторых слоях начинается растрескивание полимерного связующего, материал расслаивается.
Эти два аспекта: целесообразность применения в авиации и ракетно-космическом строительстве композитов как материалов, обладающих высокими эксплуатационными свойствами, с одной стороны, и недостаточная изученность механики их разрушения для оценки несущей способности и надежности конструкций, с другой, — определяют актуальность работы по совершенствованию технологии создания композитов.
Получение и применение композиционных материалов в авиастроении (с момента создания и до наших дней).
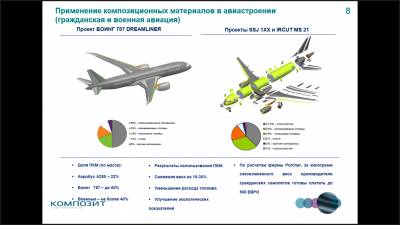
Создание перспективных образцов для авиационной, ракетно-космической техники и других отраслей промышленности, как считают многие ученые, определяется широким использованием композиционных материалов.
Конструкция из композиционного материала – это еще один шаг вперед для авиации. Огромное количество деталей конструкции самолета изготавливались и продолжают изготавливаться из стекловолокна. Конечно, сейчас мы можем найти самолеты, которые практически полностью изготовлены из стекловолокна. Технологии композиционных материалов безвозвратно изменили авиационную индустрию. Итак, рассмотрим технологию самолетостроения (с точки зрения использования композиционных материалов) и начнем с самого начала.
Русский изобретатель Александр Федорович Можайский (1825-1890) в 1882 г. построил самолет с тянущим винтом(модель «Летунья»).
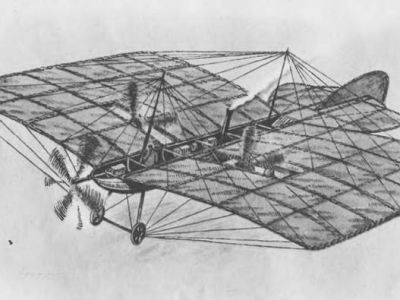
Основным конструкционным материалом для самолета предполагалось использовать стальные угловые профили общей массой 410 кг и частично — дерево. Для обшивки крыльев, хвостового оперения и палубы лодки – шелковая материя.
В 1912 г. бельгиец Арман Депердассин основал самолетостроительную компанию, где был построен гоночный самолет со сплошной обшивкой.
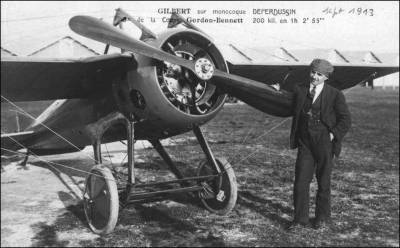
29 сентября 1913 года французский пилот Морис Прево на гоночном самолете "Депердюссен Монокок" выиграл проходившие в Реймсе авиагонки на приз американского газетного магната Гордона Беннета, развив рекордную скорость 203,86 км/ч..
Это позволило усилить и облегчить конструкцию и получить совершенно новые обтекаемые формы.
Фюзеляж был сделан из многослойного тонкого шпона тюльпанного дерева, изогнутого по определенной форме, проклеенного и покрытого пропитанной лаком материей. Если вновь обратиться к применению КМ, то можно с уверенностью сказать, что в этом самолете реализовалась идея применения новых материалов с целью обеспечения необходимых механических характеристик.
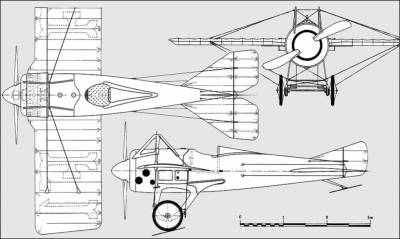
В конце 30-х годов все серийные истребители в Советском Союзе имели в своей основе смешанную конструкцию. Несмотря на все недостатки при использовании древесины (в основном — больший вес конструкций необходимой жёсткости) создание «дельта-древесины» и продвижение проекта самолёта ЛаГГ-1/ЛаГГ-3 (рис. 4), построенного с использованием этих материалов, привело к появлению на свет современного по тому времени истребителя цельнодеревянной конструкции. Фюзеляж самолета изготавливался из «дельта-древесины».
Дельта-древесина или бакелитовая фанера — конструкционный материал, получаемый пластификацией древесного шпона (обычно берёзового) путём пропитки его фенол- или крезолоформальдегидной смолой под давлением порядка 6 атмосфер и температуре 270°С, а затем склеивания или прессования. Дельта-древесина имеет всего в два раза большую, чем обычная древесина, плотность, но значительно превосходит её по прочности.
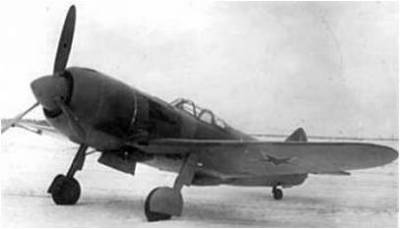
Новую модификацию истребителя , которая во второй половине 1943 г. получила обозначение Ла-5ФН, называли лучшим фронтовым истребителем второй мировой войны, не имевшим себе равных на Восточном фронте.
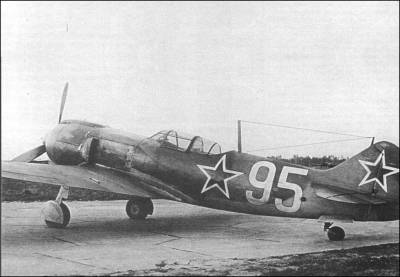
Практически в это же время британские конструкторы создали многоцелевой бомбардировщик де Хевилленд Москито.
В конструкции самолёта была применена толстая трехслойная обшивка с внешними слоями из фанеры и внутренним из бальсы с еловыми вставками для прочности, оклеенная поверх полотном. Ее использование позволило достичь достаточно большой прочности при достаточно малом весе конструкции.
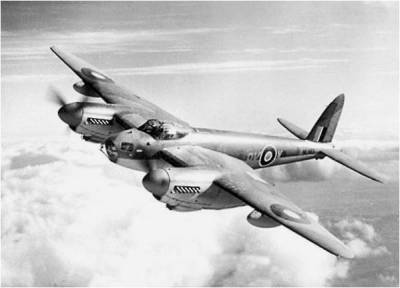
Немецкие радары были не в состоянии своевременно засекать приближающийся «Москито», так как у этого самолета только двигатели и некоторые элементы управления были сделаны из металла. «Москито» оснащались двигателями с компрессорами наддува, спроектированными для работы на больших высотах, и имели потолок до 11 000 метров.
В 80-х годах ХХ века организуется и успешно развивается целое производство композиционных материалов, которое занимается изготовлением лопастей из композиционных материалов несущих винтов вертолётов, деталей и агрегатов. Самолет АН-72 является первым отечественным самолетом, выполненным с применением различных композитов .
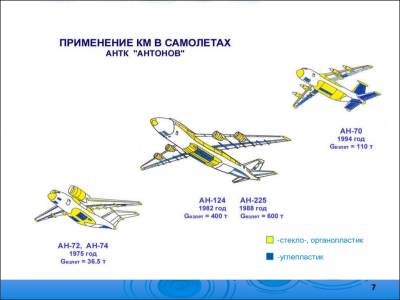
По мере того как внедрялись все новые типы конструкций, улучшался дизайн, эргономика и прочность самолета, всё большую популярность приобретали композиционные материалы.
Из графика видно,что спрос на них ежегодно растет.
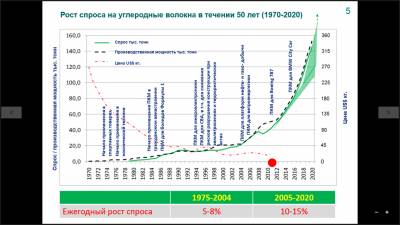
Спрос на материалы с новыми характеристиками был связан с увеличением доли композиционных материалов в технологии самолетостроения.
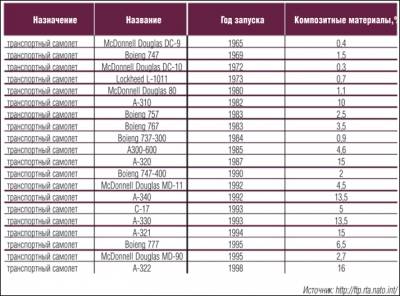
Например, использование конструкций из стеклопластика фирма «Боинг» начала уже в 1958 г.
В нашей стране аналогичные изделия появились в середине 60-х годов. На самолете-гиганте «Руслан» были установлены детали и сборочные единицы из композиционных материалов.
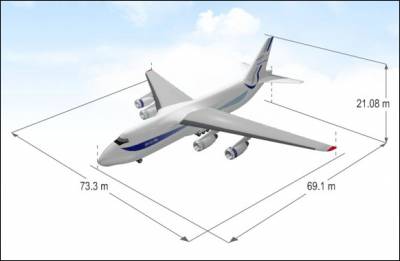
Ан-124 «Руслан» (в кодификации НАТО присвоено обозначение Condor — «Кондор») – грузовой самолёт, являющийся самым крупным серийным грузовым самолётом в истории мировой авиации.
Еще шире представлены композиты в самолетах «ИЛ-96» и «ТУ-204».
В самолете Ту-204 из композитных материалов было сделано 25% деталей, в том числе вся механизация крыла. Благодаря композитным составляющим вес Ту-204 оказался на 1200 килограммов меньше, чем был бы у аналогичной полностью металлической модели. А поскольку каждый сэкономленный килограмм веса воздушного суда снижает потребление топлива на 2–3 килограмма в год.
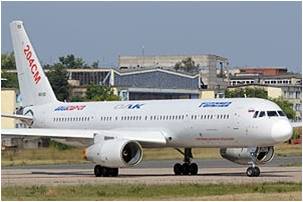
Сегодня самолетостроение всего мира от постепенного увеличения процента композитов в конструкции планера и, следовательно, постепенного накопления опыта применения новых технологий в области композитных конструкций, перешло к созданию полностью композитных самолетов.
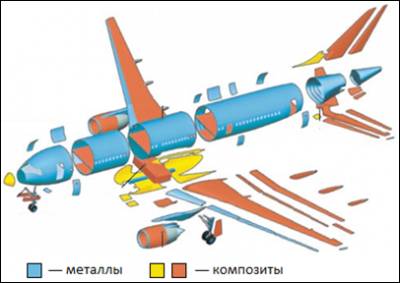
И в нашей стране имеются такие разработки , например, перспективный авиационный комплекс фронтовой авиации Т-50— российский многоцелевой истребитель пятого поколения. По массе композитные материалы составляют 25 % веса пустого самолёта, а по площади поверхности — 70 %.
Далее, самолет ИЛ-476 на 70% состоит из новых компонентов, по сравнению с предыдущими версиями Ил-76. Помимо новой силовой установки, адаптера аналоговых и цифровых систем было сделано новое композитное крыло.
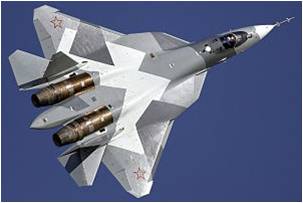
По использованию композитов в нашей стране одну из лидирующих позиций занимает ракетно-космическая промышленность. Межконтинентальная баллистическая ракета «Тополь-М» на 90% состоит из композитов (конструкции двигателей, головная часть, смесевые топлива).
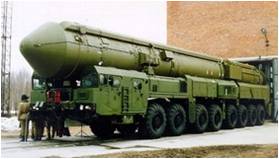
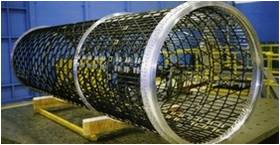
Обнинское научно-производственное предприятие (НПП) «Технология» разработало сверхпрочные сотовые композиционные материалы для авиации и ракетно-космической техники.
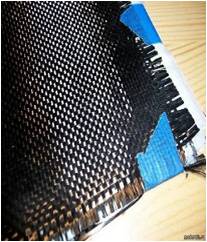
Надежность конструкций из композитов, высокие демпфирующие свойства, низкая чувствительность к концентраторам напряжений сочетаются с хорошей технологичностью.
Комбинируя объемное содержание компонентов, можно, в зависимости от назначения, получать композиционные материалы с требуемыми значениями прочности, жаропрочности, модуля упругости, абразивной стойкости, а также создавать композиционные материалы с необходимыми магнитными, диэлектрическими, радиопоглощающими и другими специальными свойствами.
Трудности создания композиционных материалов.
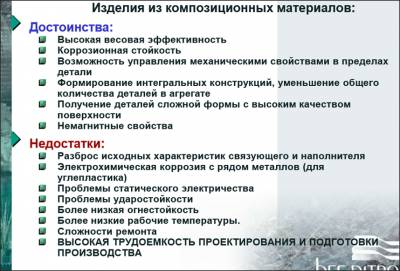
Высокая стоимость КМ обусловлена высокой наукоёмкостью производства, необходимостью применения специального дорогостоящего оборудования и сырья, а, следовательно, развитого промышленного производства и научной базы страны. Однако это справедливо лишь при замене композитами простых прокатных изделий из черных металлов. В случае легких изделий, изделий сложной формы, коррозионно-стойких изделий, высокопрочных диэлектрических изделий композиты оказываются в выигрыше. Причем стоимость композитных изделий зачастую оказывается ниже аналогов из цветных металлов или нержавеющей стали.
Анизотропия — зависимость свойств КМ от выбора направления измерения. Например, модуль упругости однонаправленного углепластика вдоль волокон в 10-15 раз выше, чем в поперечном.
Для компенсации анизотропии увеличивают коэффициент запаса прочности, что может нивелировать преимущество КМ в удельной прочности. Таким примером может служить опыт применения КМ при изготовлении вертикального оперения истребителя МиГ-29. Из-за анизотропии применявшегося КМ вертикальное оперение было спроектировано с коэффициентом запаса прочности кратно превосходящим стандартный в авиации коэффициент 1,5, что в итоге привело к тому, что композитное вертикальное оперение Миг-29 оказалось равным по весу конструкции классического вертикального оперения, сделанного из дюралюминия.
Тем не менее, во многих случаях анизотропия свойств оказывается полезной. Например трубы, работающие при внутреннем давлении испытывают в два раза большие разрывающие напряжения в окружном направлении по сравнении с осевым. Следовательно, труба не должна быть равнопрочной во всех направления. В случае композитов это условие легко обеспечить, увеличив вдвое армирование в окружном направлении по сравнению с осевым.
Низкая ударная вязкость также является причиной необходимости повышения запаса прочности. Кроме этого, низкая ударная вязкость обуславливает высокую повреждаемость изделий из КМ, высокую вероятность возникновения скрытых дефектов, которые могут быть выявлены только инструментальными методами контроля.
Высокий удельный объем является существенным недостатком при применении КМ в областях с жесткими ограничениями по занимаемому объёму. Это относится, например, к области сверхзвуковой авиации, где даже незначительное увеличение объёма самолёта приводит к существенному росту волнового аэродинамического сопротивления.
Композиционные материалы гигроскопичны, то есть склонны впитывать влагу, что обусловлено несплошностью внутренней структуры КМ. При длительной эксплуатации и многократном переходе температуры через 0 по Цельсию вода, проникающая в структуру КМ, разрушает изделие из КМ изнутри (эффект по природе аналогичен разрушению автомобильных дорог в межсезонье). Справедливости ради нужно отметить, что указанный недостаток относится к композитам первых поколений, которые имели недостаточно эффективное сцепление связующего с наполнителем, а также большой объем каверн в матрице связующего. Современные типы композитов с высокой адгезией связующего к наполнителю (достигается применением специальных замасливателей), получаемые методами вакуумного формования с минимальным количеством остаточных газовых каверн этому недостатку неподвержены, что позволяет в частности строить композитные корабли, производить композитную арматуру и композитные опоры воздушных линий электропередач.
Тем не менее КМ могут впитывать другие жидкости, обладающие высокой проникающей способностью, например, авиационный керосин или другие нефтепродукты.
При эксплуатации КМ могут выделять пары, которые часто являются токсичными. Если из КМ изготавливают изделия, которые будут располагаться в непосредственной близости от человека (таким примером может послужить композитный фюзеляж самолета Boeing 787 Dreamliner), то для одобрения применяемых при изготовлении КМ материалов требуются дополнительные исследования воздействия компонентов КМ на человека.
- Низкая эксплуатационная технологичность
Композиционные материалы могут иметь низкую эксплуатационную технологичность, низкую ремонтопригодность и высокую стоимость эксплуатации. Это связано с необходимостью применения специальных трудоёмких методов (а подчас и ручного труда), специальных инструментов для доработки и ремонта объектов из КМ. Часто изделия из КМ вообще не подлежат какой-либо доработке и ремонту.
Композиционные материалы применяются не только в авиации ,но и в космонавтике, для изготовления силовых конструкций летательных аппаратов, искусственных спутников, теплоизолирующих покрытий шаттлов, космических зондов. Всё чаще композиты применяются для изготовления обшивок воздушных и космических аппаратов, и наиболее нагруженных силовых элементов.
Дефекты структуры композита, такие как трещины, воздушные раковины, свили, отслоения волокон от матрицы, инородные включения и т.д., появляющиеся как на стадии изготовления, так и в процессе эксплуатации, существенно ослабляют его прочность. Большинство композитных материалов подвержены старению, т.е. их упругие свойства меняются под действием динамических и статических нагрузок. Такие процессы приводят к изменению затухания и скорости распространения ультразвуковых волн в композите. Поэтому одним из наиболее распространенных методов неразрушающего контроля и диагностики композитных материалов является ультразвуковой метод.
С чем связано недостаточное развитие отрасли композитов в России?
В Российской Федерации уже сложились все базовые предпосылки для формирования самостоятельной композитной отрасли, ведь вне зависимости от того где применяются изделия из композитов, основные технологические приемы их переработки остаются одними и теми же. Однако до сих пор она пребывает в зачаточном состоянии. Основные причины этому известны: технологическая отсталость отечественного производства, причем, как производства исходного сырья (смолы и армирующие материалы) так и конечных продуктов - композитных изделий;
отсутствие крупных потребителей композитных изделий в тех отраслях промышленности, где композиты способны заменить традиционные;
отсутствие действующей и работоспособной системы технического регулирования, отсутствие современных стандартов, регламентирующих производство и методы испытаний композитов.
Решение данных проблем, создаст необходимые условия по существенно более широкому применению реактопластов, армированных волокнами в различных отраслях промышленности РФ.
Заключение.
Повсеместно внедрение композитов – настоящая революция в технике. Одной из главных сфер применения композитов остается авиационная и ракетно-космическая техника.
Массу самолетов выполненных с применением композитов, можно снизить на 15-20%, что для летательных аппаратов имеет решающее значение.
Чтобы полностью реализовать потенциальные возможности снижения массы конструкций при использовании полимерных КМ, необходимо улучшить их характеристики стойкости к ударным повреждениям и расслоению ,а также обеспечить ремонтопригодность дефектных конструкций.
Несмотря на все минусы КМ, они стали идеальными для производства благодаря своей прочности, легкому весу и возможности сборки, избежав многих трудностей их соперников – металлов, дерева, бетона и других материалов. Представители промышленности стремятся найти решения, которые позволяют оптимизировать сырьевые материалы и эксплуатационные характеристики. При высоком спросе на сырьевые материалы и постоянном росте цен особую значимость приобретает техническая сторона вопроса.
Получение технологии, которая позволяет уменьшить вес и толщину деталей, и одновременно увеличить гибкость, прочность, упругость деталей меняет положение дел. И поэтому можно смело делать вывод: XXI век станет веком композитов и высоких технологий.
Список литературы.
Буланов И.М., Воробей В.В. Технология ракетных и авиакосмических конструкций из композиционных материалов. Учеб. для вузов. М.: МГТУ им. Н.Э. Баумана, 1998. -516 с.
Келли А.. Инженерный триумф углеволокон. Журнал «Композиты и наноструктуры», №1, 2009. С. 38-49.
Комиссар О.Н.. Композиционные материалы и технологии для аэрокосмической промышленности. Научный электронный журнал «Новости материаловедения. Наука и техника», №4, 2013. С. 1-4.
Кербер М. Л. Полимерные композиционные материалы. Структура. Свойства. Технологии. — СПб. Профессия, 2008. - 560 с.
Васильев В. В. Механика конструкций из композиционных материалов.— М.: Машиностроение, 1988. – 264 с.
Ощепков М.Ю. Композиты в авиационно-космической промышленности России. Композитный мир, 2010, ноябрь-декабрь. С. 46-49.
Субботин В.В., Гринев М.А. Опыт применения материалов производства ФГУП «ВИАМ» и PORCHER в конструкциях узлов и деталей авиационных силовых установок из полимерных композиционных материалов. Научный электронный журнал «Новости материаловедения. Наука и техника», №5, 2013. С. 1-7.
Капитанова Л.В. Проектирование самолетных конструкций из композиционных материалов на основе стохастических моделей: Автореф. дис. канд. техн. наук: 05.07.02 / Национальный аэрокосмический ун-т им. Н.Е.Жуковского "Харьковский авиационный ин-т". - Х., 2002. - 179л. - Библиогр.: л. 147-158.
http://www.viam.ru/. Всероссийский научно-исследовательский институт авиационных материалов. История. Конструкционные композиционные материалы.
|