Автор: Рахматуллин Эльдар Рафаэлович
Возраст: 17 лет
Место учебы: отделение СПО филиала ФГБОУ ВО «УГАТУ» в г. Кумертау «Авиационный технический колледж»
Город, регион: г. Кумертау, респ. Башкортостан
Руководитель: Бабушкина М.В., отделение СПО филиала ФГБОУ ВО «УГАТУ» в г. Кумертау «Авиационный технический колледж».
Как развивалось применение технологий 3D моделирования и прототипирования в авиастроении?
Цель работы: рассмотреть причины, по которым сегодня аддитивное производство не может быть внедрено практически в отечественном авиастроении, а также практические меры, которые должны исправить сложившуюся ситуацию.
Гипотеза: Аддитивное производство с трудом внедряется в отечественном авиастроении.
План работы:
1. Введение
2. Основная часть
2.1. История появления аддитивного производства
2.2. Классификация аддитивных технологий
2.3. Виды и процессы аддитивного производства
2.4. Примеры разработки и изготовления технологического оснащения для литейного передела (по выплавляемым моделям на АО «КумАПП»)
2.5. Аддитивные технологии для авиакосмической техники.
2.6. Перспектива аддитивного производства в России.
3. Заключение
4. Источники информации.
Введение
Технологический прогресс не стоит на месте. Ежедневно происходит усовершенствование цифровых технологий, позволяющее использовать новшества в различных сферах деятельности человека. Аддитивные технологии – одни из самых передовых и востребованных в мире.
В производстве авиационно-космической техники проявляется повышенный интерес к применению АТ. Ведущие компании мира проводят широкий круг научно-исследовательских и опытно-конструкторских работ в этой области, появляются промышленные образцы изделий АП, начат серийный выпуск ряда наименований деталей, прогнозируется расширение сферы их эффективного применения.
История появления аддитивного производства
В начале 1980-х начали развиваться новые методы производства деталей, основанные не на удалении материала как традиционные технологии механической обработки, а на послойном изготовлении изделия по трехмерной модели, полученной в САПР, за счет добавления материала в виде пластиковых, керамических, металлических порошков и их связки термическим, диффузионным или клеевым методом [1].
Группа этих технологий на западе получила название «аддитивное производство» (англ. Additive Manufacturing – от слова аддитивность - прибавляемый) – это послойное наращивание и синтез объекта с помощью компьютерных 3D технологий. Более чем за три десятилетия технология перешла от изготовления бумажных и пластиковых прототипов к непосредственному получению готовых функциональных изделий. К настоящему времени технология позволяет получать металлические и неметаллические прототипы и функциональные изделия, которые не требуют механической постобработки [2].
Аддитивные технологии (производства) (далее АТ и АП) за последние 20 лет образовали интенсивно развивающийся инновационный сегмент технологии машиностроения: достигнуты впечатляющие практические результаты, сформирован мировой рынок технологий, оборудования и услуг, развернут широкий фронт научно-исследовательских и опытно-конструкторских работ, начата подготовка квалифицированных кадров, появилась предметно ориентированная научная и учебно-методическая литература.
Два основных признака определяют этот сегмент технологий:
- признак аддитивности — конечная конфигурация изделия получается путем целенаправленного добавления дозированных объемов (масс) материала к исходной конфигурации или к подложке;
- признак виртуальности — в основе создания изделия лежит его цифровая модель.
Примеры аддитивных технологий: ковка, штамповка, гибка, обработка резанием лезвийным или абразивным инструментом, химическое растворение, селективное лазерное спекание или плавление, некоторые способы электрохимической обработки, модификации метода химических транспортных реакций, интеграция металлорежущих станков с ЧПУ с лазерной головкой и пр.
АТ обладают рядом достоинств и недостатков по отношению к классическим субтрактивным технологиям. Математическим инструментом для выявления области их эффективного практического применения является аппарат и численные средства многопараметрической оптимизации.
Определяющими факторами применения АТ, выступающими в качестве главных критериев их выбора, являются существенное сокращение длительности технологической подготовки производства новых изделий, сокращение цикла их изготовления, возможность использования принципиально новых конструкторско-технологических решений, снижение, в конечном счете, трудоемкости и себестоимости изготовления ответственной продукции. Степень гибкости аддитивных технологий достигает уровня кастомизации, то есть, способности удовлетворять индивидуальные требования потребителей продукции.
Среди применений аддитивных технологий наиболее востребовано производство функциональных изделий для наиболее заинтересованных отраслей промышленности, таких как: авиакосмическая отрасль, автомобиле- и машиностроение, ВПК, медицина в части протезирования, то есть там, где существует острая потребность в изготовлении высокоточных изделий и их прототипов в кратчайшие сроки.
Компания 3D Systems была первой компанией, которая разработала первую коммерческую стереолитографическую машину – SLA – Stereolithography Apparatus (1986 г.). До середины 90-х гг. она использовалась главным образом в научно-исследовательской и опытно-конструкторской деятельности, связанной с оборонной промышленностью. Широкое распространение цифровых технологий в области проектирования, моделирования и расчётов и механообработки cтимулировало взрывной характер развития технологий 3D-печати, и в настоящее время крайне сложно указать область материального производства, где в той или иной степени не использовался бы 3D-принтер [3].
Классификация аддитивных технологий
В работе все технологии рассматриваются с точки зрения производства именно металлических деталей конструкции воздушных судов. Изготовление металлических изделий — это последовательность технологических процессов формообразования и обработки металла или сплава.
В рассматриваемых источниках представлены многочисленные классификационные модели аддитивных технологий. Так, по классификации ASTM аддитивные технологии разделены на 7 групп:
- Material Extrusion — выдавливание материала или послойное нанесение расплавленного строительного материала через экструдер;
- Material Jetting — разбрызгивание (строительного) материала или послойное струйное нанесение строительного материала;
- Binder Jetting — разбрызгивание связующего или послойное струйное нанесение связующего материала;
- Sheet Lamination — соединение листовых материалов или послойное формирование изделия из листовых строительных материалов;
- Vat Photopolymerization — фотополимеризация в ванне или послойное отверждение фотополимерных смол;
- Powder Bed Fusion — расплавление материала в заранее сформированном слое или последовательное формирование слоев порошковых строительных материалов и выборочное (селективное) спекание частиц строительного материала;
- Directed energy deposition — прямой подвод энергии и материала непосредственно в место построения или послойное формирование изделия методом внесения строительного материала непосредственно в место подвода энергии [11].
Эта классификация аддитивных технологических методов производства деталей, приведенная в стандарте ASTM F2792.1549323-1 (США), в значительной степени устарела за последние двадцать лет в связи с бурным развитием технологического оборудования. В 2015 г. приказом Росстандарта создан технический комитет «Аддитивные технологии» для разработки терминов, определений и стандартов, относящихся к ним.
Разработка классификации аддитивных технологий с учетом разнообразия применяемых методов, материалов и оборудования является достаточно сложной задачей. В международном сообществе, так же, как и в России, устоявшейся классификации аддитивных технологий пока не принято.
По принципу формирования детали (нанесения слоя) следует выделить два направления развития аддитивных технологий.
Первое направление. Формирование детали происходит путем объединения материала, распределенного на рабочей поверхности платформы технологического оборудования (Bed deposition) (рис. 1). После окончания процесса изготовления остается некоторый объём материала, который может использоваться для формирования следующей детали. Процессы объединения материала, распределенного на платформе, заложены в основу различных видов технологического оборудования для производства деталей методами аддитивных технологий.
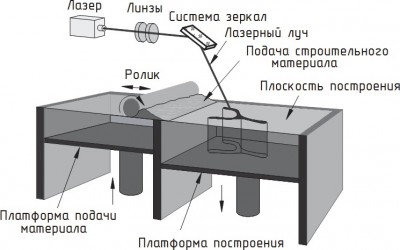
Рисунок 1. Схема получения детали путем объединения материала,
распределенного на рабочей поверхности
По методу фиксации слоя выделяют три способа: фотополимеризация, сплавление (спекание), склеивание (рис. 2).
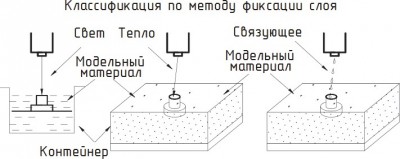
Рисунок 2. Классификация аддитивных технологий по способу фиксации слоя:
а – фотополимеризация (свет); б – сплавление (тепло); в – склеивание (связующее)
Фотополимеризация. По данному методу выделяют несколько технологий получения изделия.
Стереолитография (SLA-технология). Принтеры, работающие по данному принципу, имеют платформу, которую погружают в бак с жидким фотополимером. Лазер проходит по поверхности, в результате чего слой фотополимера затвердевает. Затем платформа опускается на глубину одного слоя и процесс повторяется до тех пор, пока объект полностью не построится. Материал, использующийся в SLA-технологиях, – фотополимерная смола.
Технология PolyJet. Нанесение материала происходит с помощью струйных головок. Жидкий фотополимер отвердевает под действием светового излучения. После окончания нанесения всего слоя зону печати подвергают мощному ультрафиолетовому излучению для полного отвердевания материала, после чего наносится следующий слой. Для примера, с помощью современных 3D-принтеров Object 350 в данной технологии могут применяться до семи различных фотополимеров, которые отличаются физическими свойствами.
Сплавление (спекание). В качестве примера можно рассмотреть селективное лазерное спекание (SLS-технологии). В принтерах, работающих по такой технологии, сначала формируется слой материала, после чего происходит выборочное спекание порошка лазером, связывая частички порошка в соответствии с текущим сечением исходной модели. В качестве исходного материала SLS-технологии используются полимерные и керамические порошки и термопластики. Так как плавление материала происходит выборочно по заданной траектории, то достоинством этой технологии является возможность одновременного производства нескольких деталей, что приводит к повышенной производительности всего аддитивного процесса.
Виды и процессы аддитивного производства
Существует несколько видов технологий аддитивного производства, которые мы рассмотрим.
Selective Laser Melting (SLM)
Selective Laser Melting (SLM) – это процесс селективного лазерного плавления, повышение эффективности которого возможно за счёт оптимального выбора стратегии обработки лазерным лучом. Метод селективного лазерного плавления представляет собой процесс послойного сплавления деталей из металлического, керамического или полимерного порошкового материала.
Технология SLM включает в себя:
- подготовку трёхмерной модели изделия в компьютерной среде;
- нанесение порошка на рабочую платформу распределителем порошка, формирующим слой толщиной 20-40 мкм;
- очерчивание контура и выборочное расплавление порошка лучом лазера высокой мощности, движущимся в каждом слое по определённой траектории в соответствии с выбранной стратегией обработки и согласно трёхмерной модели изделия в компьютерной среде. Процесс повторяется для каждого слоя, до полного формирования изделия.
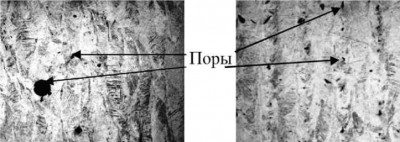
Рисунок 3 - Дефекты – поры в срезе образца изделия,
полученного при помощи метода селективного лазерного плавления
Electron Beam Melting (EBM)
Electron Beam Melting (EMB) – это процесс электронно-лучевой плавки, основой которого является термоэлектронный излучатель, использующий вольфрамовую нить для создания пучка электронов. Сканирующий пучок выборочно плавит металлический порошок (с толщиной слоя 70-250 мкм), вызывая его спекание. Порошок, спекшийся вокруг изделия, обеспечивает опору для поверхностей, направленных книзу, а в процессе постобработки счищается, тем самым сохраняя большую часть не подвергшегося спеканию порошка для повторного использования.
Процесс ЕВМ выгодно отличается от лазерных процессов более высокой скоростью сканирования, что сокращает время изготовления изделия, и меньшими термическими напряжениями. Однако круг используемых материалов ограничен проводящими электрический ток металлическими порошками, а качество поверхности изделия уступает результату лазерных процессов.
Direct additive laser construction (CLAD) – это технология прямого лазерного аддитивного построения, применяемая исключительно на промышленном уровне ввиду сложности и относительно узкой специализации.
В основе CLAD лежит напыление металлического порошка на поврежденные детали с немедленной наплавкой с помощью лазера. Металлический порошок определенной фракции через специальную головку подается непосредственно в место построения. Далее порошок под воздействием энергии лазерного излучения расплавляется и кристаллизуется. Процесс построения изображен на (рис. 4). Суммарное количество степеней свободы при изготовлении или ремонте детали равняется пяти.
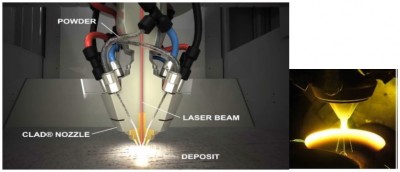
Рисунок 4. Процесс построения детали по технологии CLAD
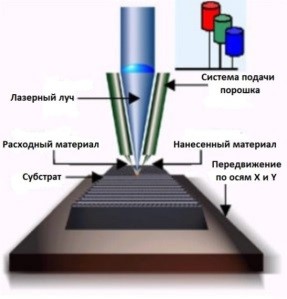
Рисунок 5. Схема работы установок, использующих технологию CLAD
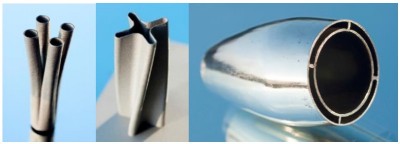
Рисунок 6. Изделия, изготовленные по технологии CLAD
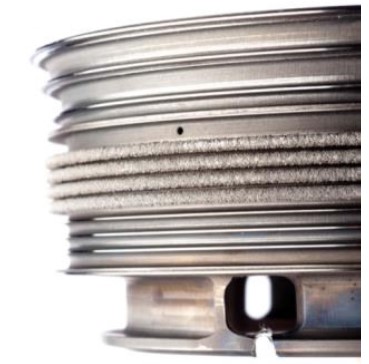
Рисунок 7. Лабиринтное уплотнение, отремонтированное с помощью технологии CLAD
Direct Manufacturing (DM)
- Direct Metal Deposition (DMD). Процесс прямого нанесения металлов является разновидностью технологии лазерного нанесения металлов (LMD, Laser Metal Deposition).
- Direct Metal Laser Sintering (DMLS). Процесс прямого лазерного спекания металлов требует использования связующих веществ с температурой плавления ниже, чем у основного металлического компонента. В качестве таких связующих материалов могут использоваться полимерные порошки, которые выжигаются из изделия при последующей обработке, либо металлические порошки с более низкой точкой плавления. В отличие от чистых металлов, плавление которых происходит одновременно по всему объему, у легированных металлических порошков есть диапазон температур, в котором в процессе плавления/затвердевания жидкая и твердая фаза сосуществуют.
Direct Metal Printing (DMP)
DMP – название аддитивной технологии PBF по классификации ASTM, используемое компанией 3D Systems Corp. (бывшая Phenix Systems) (США).
Electron Beam Direct Manufacturing (EBDM)
EBDM – название аддитивной технологии DED по классификации ASTM, используемое компанией Sciaky Inc. (США).
Electron beam freeform fabrication (EBF3). Произвольная электронно-лучевая плавка (EBF3) (рис. 8) – технология, разрабатываемая специалистами НАСА для применения в условиях невесомости (рис. 9). Отсутствие гравитации делает работу с металлическими 7порошками практически невозможной, поэтому технология EBF3 подразумевает использование металлических нитей.
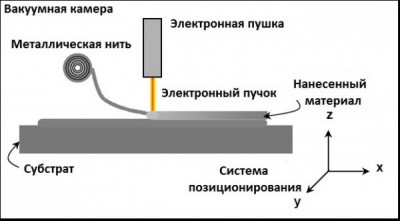
Рисунок 8. Схема работы EBF3 принтеров
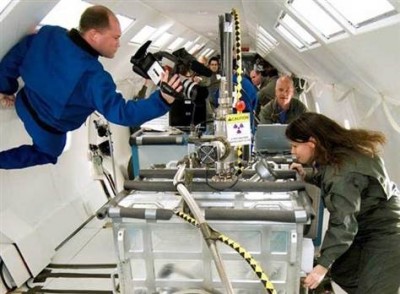
Рисунок 9. Специалисты НАСА проводят испытания прототипа EBFȝ
в условиях искусственной невесомости
Процесс построения схож с 3D-печатью методом послойного наплавления (FDM), но с использованием электронно-лучевой пушки для плавки расходного материала. Данная технология позволяет создавать металлические запасные части на орбите, что существенно сокращает затраты на доставку частей и обеспечивает возможность быстрого реагирования на внештатные ситуации.
Fused Deposition Modeling (FDM)
Сущность изготовления объектов путем послойной наплавки заключается в том, что материал расплавляется в разогретом сопле-дозаторе, движениями которого непосредственно управляет программное обеспечение системы автоматизации производства. После экструзии из сопла, материал остывает и затвердевает. Изделие формируется последовательным нанесением слоев материала. Поскольку материал нагревается до температуры лишь на 1°С превышающей температуру плавления, он становится твердым практически сразу после экструзии, соединяясь с предыдущими слоями.
Laminated Object Modeling (LOM)
В настоящее время принципы ламинирования листовых материалов путем «соединение – раскрой» успешно применяются для изготовления деталей из металла, керамики и композитных материалов. В качестве строительного материала для формирования полуфабрикатов применяются керамонаполненные или металлонаполненные ленты, затем полуфабрикаты подвергаются постобработке в печи при высокой температуре для склеивания и спекания материала изделия. Эти ленты затем используются для построения изделий путем стандартного процесса ламинирования листовых материалов. Плюсом данной технологии является относительная дешевизна производства и высокое визуальное сходство получаемых моделей с цельнометаллическими изделиями. Как правило, этот метод используется для макетирования.
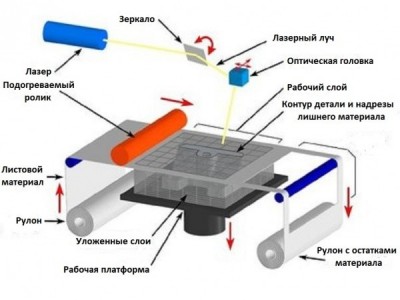
Рисунок 10. Схема работы 3D-принтеров, использующих технологию LOM
Laser Engineered Net Shaping (LENS)
На сегодняшний день технология LENS (рис.11) является наиболее совершенной (по достижимому уровню прочностных характеристик создаваемых объектов) реализацией метода послойного воспроизведения. Данный метод позволяет применять в качестве модельных материалов практически любые металлы и сплавы, которые могут быть расплавлены лазерным лучом без испарения. Создаваемые детали имеют ультрамелкозернистую структуру и в ряде случаев по своим механическим свойствам значительно превосходят изделия, получаемые из аналогичных сплавов традиционными методами.
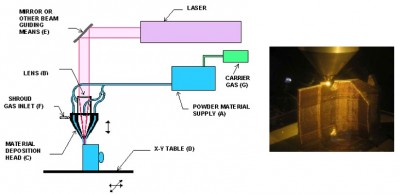
Рисунок 11. Технология LENS
Stereolithography (SL)
Сущность процесса стереолитографии заключается в:
- моделировании детали и преобразовании в файл формата STL для создания объемной полигональной сетки и поддерживающей структуры;
- нарезке трехмерной модели в STL-формате для создания набора сечений;
- передаче рассеченной модели в стереолитографический аппарат (SLA);
- послойном формировании детали и поддерживающей структуры в ванне со специальным полимером с помощью аргонового лазера, который очерчивает двумерные сечения и приводит к отвердеванию полимера;
- удалении поддерживающей структуры и, при необходимости, последующим отвердевании детали для окончательной полимеризации посредством управляемого обогрева или в УФ-печи.
Стереолитография часто используется для быстрого прототипирования и быстрого изготовления инструментальной оснастки с целью создания пресс-форм и форм для литья. Основным ограничением процесса стереолитографии является потребность в поддерживающей структуре, что увеличивает расходы материала и удлиняет производственный цикл.
StereoLithography Apparatus (SLA)
Стереолитография (лазерная стереолитография, SLA) – первая технология аддитивного производства, запатентованная в 1986 г. Ч. Халлом. Созданный под эту технологию формат .STL до сих пор используется в сфере трехмерной печати.
Среди преимуществ данной технологии: неограниченные возможности геометрии объектов; точность и высокое качество поверхности (минимальная толщина слоя SLA принтеров доходит до 0,025-0,05 мм); высокая скорость работы 3D-принтеров и экологичность (отсутствие отходов). К недостаткам относят высокую стоимость принтеров (бюджетные принтеры, работающие по технологии SLA, такие как FORM 1 или Pegasus Touch, были выпущены совсем недавно). Целесообразность применения этой технологии обусловлена сложностью модели, необходимыми техническими свойствами объекта, объемом производства и т.п.

Рисунок 12. Технология SLS
Solid Ground Curing (SGC)
Технология SGC – версия SLA-технологии, в которой материал засвечивается не лазером, а ультрафиолетовой лампой. Технология обладает достаточно высокой точностью в Z-направлении, но большое количество отходов при фрезеровании слоев и высокие эксплуатационные затраты на сложную конструкцию принтера повышают стоимость печати. Важнейшее преимущество технологии SGC – возможность остановить процесс печати в любой момент и потом возобновить его без каких-либо потерь. Технология позволяет обходиться без подпорок и не требует дальнейшей обработки модели. Метод позволяет создавать модели с движущимися элементами. К недостаткам технологии относится необходимость в специфических дорогостоящих полимерах[4].
Преимущества 3D-печати:
- Изготовление деталей с геометрией любой сложности, что оставляет далеко позади возможности традиционных методов.
- Оптимизация таких параметров изделий, как точность и прочность, а также снижение массы за счет создания супертонких стенок, внутренних каналов и бионических структур.
- Ускорение и снижение стоимости производственного процесса: нет необходимости использовать дорогостоящую оснастку, а в отдельных случаях – механообработку.
- Повышение рентабельности изготовления мелкосерийной и кастомизированной продукции.
- Снижение рисков и ошибок проектирования, в том числе за счет возможности изменения конструкции на поздних этапах проектирования.
- Управление физико-механическими свойствами продукта благодаря использованию высокотехнологичных материалов.
Задачи, решаемые в машиностроении с помощью 3D-печати:
- Функциональное тестирование и прототипирование.
- Изготовление технических прототипов для отработки конструкции изделий.
- Проведение технологических экспериментов.
- Проверка изделий на эргономичность.
- Создание мастер-моделей для литья, в том числе по выплавляемым и выжигаемым моделям.
- Быстрое изготовление оснастки.
- Производство формообразующих элементов пресс-форм для литья термопластов и легких материалов.
- Изготовление функциональных деталей для разнообразных агрегатов и узлов.
- Создание сложных конструкций, в том числе цельных, которые ранее собирались из многих элементов.
Практические примеры разработки и изготовления технологического оснащения для литейного передела
При освоении новых изделий на действующих предприятиях одним из этапов работ является разработка, изготовление технологического оснащения (в частности для литейного передела). Необходимо, отметить, что изготовление оснастки по существующим технологиям является сложным и трудоемким процессом, требующим длительных, порой неоднократных, ручных доработок и измерений, выполняемых специалистами высокого класса.
В городе Кумертау на АО «КумАПП» с 2017-2019 г.г. проводились опытные работы, включающие комплекс организационных и технических мероприятий по изготовлению новых изделий по аддитивным технологиям одноразовых выжигаемых моделей с использованием существующего оборудования для литья по выплавляемым моделям, направленный на снижение сроков и себестоимости освоения новых изделий.
Работы включали в себя следующие этапы:
- Анализ и выбор технологии 3D-печати.
- Разработка 3D-моделей отливки и стояка. Компьютерное моделирование технологического процесса литья детали.
- 3D-печать выжигаемых моделей.
- Изготовление отливок.
- Исследования.
В качестве изготавливаемого образца была выбрана деталь 800.20.1925.0541 «Кронштейн». Данная деталь входит в состав колонки изделия «800». Может изготавливаться только методом литья из-за наличия сложной внутренней геометрии (рис.13).
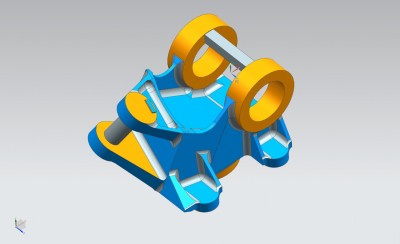
Рисунок 13. Кронштейн
Характеристика работ:
Работа состояла из 2-х основных этапов – изготовления опытного образца отливки на деталь и изготовления опытной партии.
Изготовление опытного образца включает следующие этапы:
- Разработка 3D-модели отливки с ЛПС. (АО «КумАПП»)
- Печать на 3D-принтере выжигаемой модели отливки с ЛПС по FDM или иной технологии по созданной 3D-модели отливки. (Исполнитель договора)
- Контроль геометрии выжигаемой модели на координатно-измерительной машине (далее КИМ) или при помощи оптического 3D сканера. (Исполнитель договора)
- Изготовление образца отливки по существующей технологии литья по выплавляемым моделям заказчика. (АО «КумАПП»)
- Контроль геометрии изготовленной отливки на КИМ или при помощи оптического 3D сканера. (АО «КумАПП» или Исполнитель договора)
- Проведение исследований отливки на соответствие параметров нормативной документации: марка материала, рентгенконтроль, магнитопорошковый контроль. (АО «КумАПП»)
- Корректировка технологии 3D-печати, параметров печати, материала, геометрии или ЛПС выжигаемой модели в случае отклонения от параметров нормативной документации по результатам исследований и контроля геометрии. Работы проводить до получения отливки с показателями, соответствующими нормативной документации. (АО «КумАПП», Исполнитель договора)
- При соответствии результатов исследований отливки нормативной документации переход к изготовлению опытной партии.
В реальных условиях производства на АО «КумАПП» были экспериментально подтверждены рассмотренные ранее предположения об эффективности применения аддитивных технологий для изготовления выжигаемых моделей фасонного литья из высокопрочных легированных сплавов.
Применение данной технологии позволяет снизить трудоемкость изготовления технологического оснащения, а также сократить сроки освоения новых изделий при обеспечении требуемой точности изготовления и качественных характеристик сложных отливок из высокопрочных легированных сплавов с использованием существующего оборудования литья по выплавляемым моделям.
В результате выполнения работ были получены данные, позволяющие сделать следующие выводы:
- Отработан метод компьютерного моделирования технологического процесса литья детали.
- Технология FDM позволяет получать методом 3D-печати выжигаемые модели, соответствующие требованиям по качеству поверхности, зольности, прочностным характеристикам материала.
- Разработана технология изготовления отливок методом литья по выжигаемым моделям.
- Преимущество данной работы состоит в том, что использованием 3D-технологий позволяет обеспечивать стабильность геометрии, высокое качество поверхности и структуры отливок, а также возможность оперативно вносить коррекцию в геометрию модели.
Аддитивные технологии для авиакосмической техники
В производстве авиакосмической техники аддитивные технологии обеспечивают следующие основные преимущества:
1. Стоимость вывода 1 кг массы на орбиту Земли составляет от 12 до 25 тыс. долл. Поэтому возможность снижения массы изделия за счет повышения его конструктивной сложности является весьма актуальной для ракетно-космического машиностроения.
Анализ, проведенный в рамках проекта ATIKINS, показал, что снижение массы магистрального самолета на 100 кг на протяжении всего жизненного цикла влечет за собой экономию $2,5 млн на топливных расходах и сокращает выбросы углекислого газа на 1,3 млн тонн.
Однако степень усложнения конструкции изделия ограничивается возможностями существующих методов, технологий на их основе и средств технологического оснащения. Так, аддитивные технологии обеспечивают получение системы полостей произвольной формы в теле детали, а субтрактивные — нет. Поэтому в последнем случае приходится использовать дорогостоящие заготовительные технологии с относительно низким уровнем технологической надежности и удорожанием производства из-за брака. В качестве примера рассмотрим одну из основных, лимитирующих деталей газотурбинного двигателя — лопатку турбины (рис. 14).
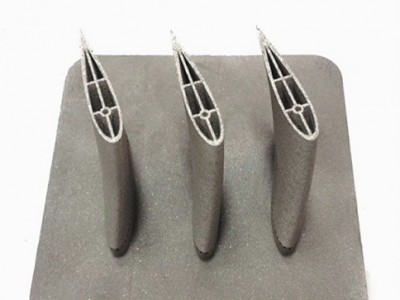
Рисунок 14 – Сечения лопатки турбины ГТД
Лопатку с сечениями, формирующими магистраль подачи охлаждающего воздуха, получают литьем по выплавляемым моделям. Отверстия для входа воздуха на передней кромке лопатки изготовляют малопроизводительным электроэрозионным прошиванием с последующей доводкой абразивной суспензией. К настоящему времени созданы опытно-экспериментальные образцы лопаток с применением SLS и SLM — технологий.
2. Коэффициент использования материала (КИМ) при традиционном производстве основных деталей двигателей авиакосмической техники составляет 0,05–0,2. Применение АТ позволяет повысить этот коэффициент до 0,7–0,9, что обеспечит значительное сокращение затрат на дорогостоящие материалы. Значение КИМ при изготовлении металлических деталей с применение АТ определяется, главным образом, массой поддержек, подлежащих удалению.

Рисунок 15 - Вариант конструкции поддержек соединительного блока
3. Сокращение длительности цикла и стоимости технологической подготовки производства новых изделий имеет первостепенное значение, особенно в опытно-экспериментальном производстве. С развитием АТ опытно-конструкторские организации могут не только осуществлять быстрое натурное моделирование составных частей опытного изделия, но и значительно ускорить как изготовление сложных деталей, так и введение изменений в их конструкции в процессе доводки и испытаний изделия. Так, по данным ОАО КБХА применение АТ при изготовлении 5 основных деталей двигателя позволяет в среднем сократить цикл изготовления в 5 раз.
4. Замена сборочной единицы деталью одного наименования повысит надежность составной части изделия и также сократит цикл ее изготовления. Так, на рис. 15 показан соединительный блок, который при традиционном исполнении представляет собой сборочную единицу, состоящую из 8 наименований деталей.
АП смесительной головки позволяет сократить число наименований деталей с 138 при классической технологии до 1–3 при АП.
5. Основные детали горячей части двигателей современных летательных аппаратов, работающие, как правило, в экстремальных условиях, изготавливают из материалов с низкой обрабатываемостью резанием, поэтому понятен интерес создателей ГТД и ЖРД к АТ, позволяющим в ряде случаев снизить трудоемкость и себестоимость технологии. Так, компания GE Aviation часть деталей нового двигателя LEAP производит с применением АТ (рис. 16).
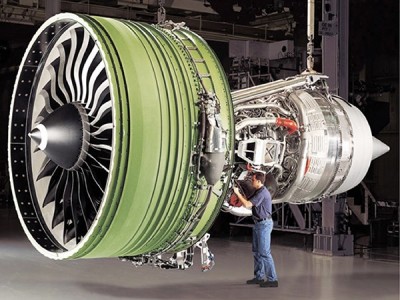
Рисунок 16. Двигатель LEAP компании GE Aviation
Технологии послойного наложения расплавленной полимерной нити позволяют использовать материалы производственного класса для изготовления деталей, работающих в условиях воздействия агрессивной среды и высоких температур. Среди продукции, созданной по данной технологии, особо важной для ОПК считается изготовление боевых беспилотных летательных аппаратов (БЛА) и учебных «дронов». К конкретным примерам относятся кронштейны видеокамер для наступательных БЛА Taranis компании BAE Systems, антенны и «дроны» двойного назначения RDASS 4 компании Leptron. В 2014 году БЛА, построенный по технологии FDM, представлен специалистами Шеффилдского университета (рис.17).
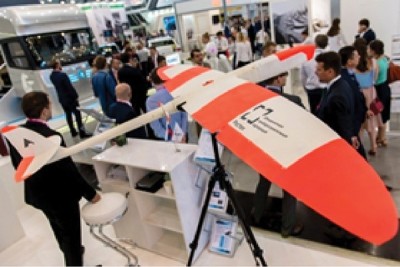
Рисунок 17 – Беспилотный летательный аппарат, созданный на основе АТ
Подобные работы проводятся и в нашей стране. ОАО «КБ «Луч», входящим в состав государственной корпорации «Ростех», создан экспериментальный образец беспилотного летательного аппарата, планер которого изготовлен с использованием аддитивных технологий. Возможности аддитивного производства обеспечили значительную экономию финансовых средств и времени на создание финального образца беспилотной авиационной техники, а также перспективы изготовления (восстановления повреждений) непосредственно в районе боевых действий [5].
Специфика применения 3D-технологий в авиакосмической отрасли:
Жесткая процедура сертификации. Качество детали, полученной путем селективного лазерного плавления, определяется четырьмя основными факторами:
- Качество 3D-принтера. Обеспечивается: проведением и анализом тестовой работы перед отгрузкой оборудования клиенту, а затем на территории клиента после установки оборудования, и регламентацией процедур калибровки и технического обслуживания.
- Качество процесса построения детали. Обеспечивается: регламентированием технологических параметров процесса и настроек оборудования.
- Качество работы с оборудованием. Обеспечивается: регламентированием процедур работы с оборудованием и внешних условий помещения для работы оборудования; уровнем подготовки операторов аддитивной установки.
- Качество используемого материала. Обеспечивается: входным контролем и тестированием материала, регламентированием процедур хранения, транспортировки, работы с материалом.
Исходя из этого, можно представить, каким трудоемким может быть процесс сертификации по всем этим четырем параметрам для получения сертифицированной детали.
Другая важная особенность применения технологии селективного лазерного плавления, в авиакосмическом секторе в частности, – работа с такими технологически трудными материалами, как сплавы титана и никеля. Эти сплавы склонны к образованию остаточных напряжений, приводящих к короблению деталей и даже трещинам [6].
Перспективным направлением в развитии аддитивных технологий в авиастроении является бионический дизайн.
Многие крупные компании, занимающиеся 3D-печатью или применяющие ее, для реализации своих разработок, давно взяли бионический дизайн на вооружение и все чаще к нему прибегают, разрабатывая свои продукты. Бионический (топонимический, генеративный) дизайн — способ проектирования различных объектов, при котором для снижения веса и увеличения прочности применяются отличные от традиционных решений.
Не секрет, что компания Airbus делает уверенные шаги в сторону проектирования самолетов будущего – в компании уже давно активно применяют 3D-печать, порождающее проектирование и другие технологии для создания отдельных деталей и даже планируют напечатать самолет целиком. Важным этапом на этом пути стало создание первой в мире бионической перегородки совместно с Autodesk.
Все началось в 2011 году, когда в компании Airbus рассказали, как будут выглядеть полеты будущего. Центральное место в них займет совершенно новый вид пассажирского самолета, который появится к 2050 году. Его крылья смогут менять форму, чтобы избежать турбулентности, а корпус будет абсолютно прозрачным. Кроме того, полеты станут более экологичными – вес самолета сильно уменьшится. Это значит, что он будет использовать меньше топлива, сократив таким образом не только объем выбросов CO2 в атмосферу, но и себестоимость полетов. Такие легкие конструкции уже сегодня являются одной из приоритетных задач проектировщиков самолетов.
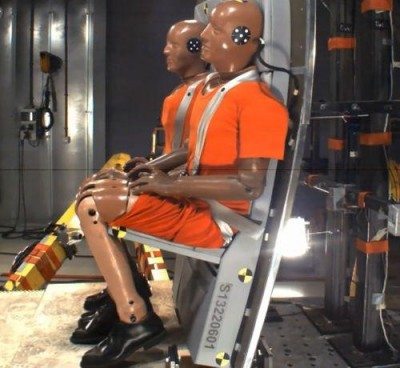
Рисунок 18. Перегородка из технологий будущего и слизевого гриба
Представив концепт самолета будущего, команда решила воплотить в жизнь хотя бы одну из его частей, используя современные технологии. Для этого была выбрана перегородка – неприметный, но крайне важный элемент, отделяющий кабину экипажа от салона пассажиров.
При проектировании этой детали, находящейся в хвостовой части самолета, обычно возникает ряд сложностей. Перегородка должна быть легкой и в то же время прочной, чтобы выдерживать вес стюардесс, которые во время взлета и посадки сидят на прикрепленных к ней откидных стульях.
По замыслу команды, новая перегородка должна была стать легче на 30% и при этом сохранить прежнюю прочность. Кроме того, она должна иметь выемку для передачи широких предметов в и из кабины, быть не более 3 см толщиной и крепиться к авиационной конструкции всего лишь в четырех местах.
Чтобы выполнить эти задачи, необходимо было использовать современные технологии вместо традиционных инженерных методов. Для этого в 2015 году Airbus объединился с Autodesk, мировым лидером в области технологий трехмерного проектирования. Совместно они использовали технологию порождающего проектирования (generative design) и 3D-печать, чтобы создать бионическую перегородку.
Порождающее проектирование – технология, которая позволяет задать компьютеру идею, уточнить функционал и технологические ограничения. Используя облачные вычисления, ПО для порождающего проектирования быстро изучает тысячи или даже миллионы вариантов дизайна, тестируя конфигурации и запоминая из каждой итерации, что работает, а что – нет. В результате проектировщик получает ответы в формате готовых решений.
Чтобы найти самый подходящий вариант дизайна и оптимизировать конструктивный скелет, команда запрограммировала ПО для порождающего проектирования Autodesk Within алгоритмами, основанными на двух растительных паттернах, существующих в природе: слизевом грибе и костях млекопитающего.
Слизевой гриб – одноклеточный организм, который умеет создавать прочные соединения между двумя статичными точками. В результате получился дизайн с решетчатой структурой, которая выглядит случайной. На самом деле такая конструкция сделана специально, делая перегородку легкой и прочной. Перегородка с бионическим дизайном весит около 30 кг, что на 45% легче, чем традиционные перегородки.
Для производства перегородки было решено применить 3D-печать, используя инновационный материал Scalmalloy – специальный состав сплава алюминия, магния и скандия, разработанных Airbus. Важно понимать, что сегодня промышленные 3D-принтеры могут печатать только небольшие детали. Для производства больших элементов необходимы более мощные и быстрые 3D-принтеры. В данном случае вся перегородка была разбита на 116 частей, каждая из которых имела элементы соединений. Было сделано по меньшей мере семь загрузок принтера, чтобы собрать единую перегородку. Бионическая перегородка, получившаяся в результате, является крупнейшим в мире 3D-напечатанным компонентом кабины самолета, и полностью отвечает требованиям: она более прочная, тонкая и легкая чем та, которую она заменит.
Создание бионической перегородки с помощью порождающего проектирования и 3D-печати стало первым шагом к экологичным полетам будущего, будет сэкономлено 3 180 кг топлива за год.
Перегородка - относительно небольшая часть самолета, но ее уменьшение может создать позитивную разницу для окружающей среды. Снижение веса самолета только на 1 кг помогает сократить расход топлива на 106 кг за год. А бионическая перегородка примерно на 30 кг легче, чем стандартная. Что сократит выброс СО2 с каждого самолета сократится на 166 тонн.
Если бионические перегородки будут установлены по всей кабине самолета Airbus A320 – то есть четыре на один самолет – это позволит снизить его вес на 500 кг. В результате сокращения расходов топлива выбросы СО2 снизятся на 166 тон в год с каждого самолета. После того как данная технология будет применяться для создания всех кабин самолетов A320, компания сократит ежегодный выброс СО2 более чем на 465 тыс. тонн, что равнозначно выбросам, которые делают порядка 96 тыс. автомобилей в течение года.
Использование 3D-печати также поможет изменить влияние на окружающую среду. При этом процессе используется только 5% от сырья (на 95% меньше сырьевого материала), которое применяется при традиционном процессе фрезерования деталей из металлического блока. Кроме того, 3D-печать позволяет повторно использовать любые материалы для производства других частей самолета.
Airbus не собирается останавливаться на достигнутом. В планах компании - создать 3D-напечатанную стену кабины экипажа, которая в два раза больше перегородки и должна быть пуленепробиваемой для защиты пилотов. Алгоритмы, основанные на характеристиках человека для проектирования сверхсильных вертикальных стабилизаторов или компонентов реактивного двигателя, тоже могут стать реальностью. Следующее поколение самолетов Airbus – с компонентами, созданными с помощью порождающего проектирования, 3D-печатью и инновационными материалами – еще больше приблизят нас к тому самому бионическому самолету 2050 года.
Перспективы аддитивного производства в России
В одной из наиболее передовых отраслей отечественного машиностроения — авиационной, хотя и имеется опыт практического использования аддитивных технологий, реальное их применение крайне ограничено.
АО "ОДК-Климов” разрабатывает перспективный вертолетный двигатель (ПДВ), при его изготовлении максимально использована 3D-печать металлами и полимерными конструкционными материалами. Представление демонстрационного образца обещано к 2021 году, окончание разработки — к 2025. Ожидается уменьшение массы двигателя на 15% и экономия средств в эксплуатации на 30% по сравнению с существующими аналогами [8].
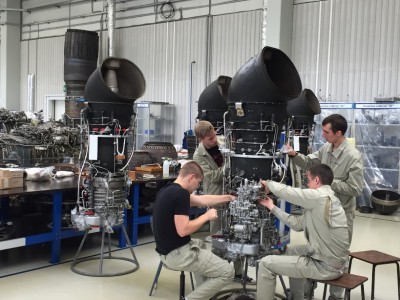
Рисунок 19. Сборочный цех АО «ОДК-Климов», сентябрь 2016
АО «ММП имени В.В. Чернышева» входит в состав Объединенной двигателестроительной корпорации и специализируется на производстве и ремонте комплектующих для авиадвигателей. В сотрудничестве с другими предприятиями Корпорации («ОДК-Сатурн», «ОДК-Пермские моторы») завод применяет 3D-печать, осуществляя НИОКР и опытное производство, внедряя образовательные программы и разрабатывая нормативную документацию. В Центре аддитивных технологий компании действует полный лабораторно-исследовательский комплекс печати из различных сплавов. Предприятие представило несколько практических результатов аддитивного производства:
- завихритель двигателя получил сертификат и будет серийно изготавливаться в «ОДК-Пермские моторы»;
- часть деталей для макета двигателя РД-33МА напечатаны на 3D-принтере;
- корпус топливного насоса с конструкцией, оптимизированной под 3D-печать, будет серийно производиться с 2020 г. [9].
При этом, если в отечественном авиационном двигателестроении есть примеры послойного синтеза опытных образцов готовых изделий, то в производстве самолётов и вертолётов аддитивные технологии если и применяются, то в основном при изготовлении технологической оснастки для изготовления элементов конструкции со сложной геометрией поверхности — штампов, пресс-форм и т. п. Примеры же непосредственного послойного синтеза элементов конструкции крайне редки и ограничиваются изготовлением аналогов сварных элементов топливной и гидравлической систем, элементов интерьера и других неответственных деталей.
Современные аддитивные технологии позиционируются их разработчиками и поставщиками как технологии промышленного производства готовых деталей или полуфабрикатов высокой степени готовности из полимерных материалов, металлических материалов или их композиций с неметаллическими материалами.
Сравним уровень современных аддитивных технологий и традиционных технологий изготовления металлических деталей — ранжируем литейное производство (1), порошковую металлургию (2), процесс «литьё — ковка / штамповка — термообработка — механическая обработка давлением, резанием — финишная обработка» (3), аддитивные процессы спекания (4) и аддитивные процессы сплавления (5) по пятибалльной шкале (по количеству групп), рассматривая их с точки зрения различных параметров.
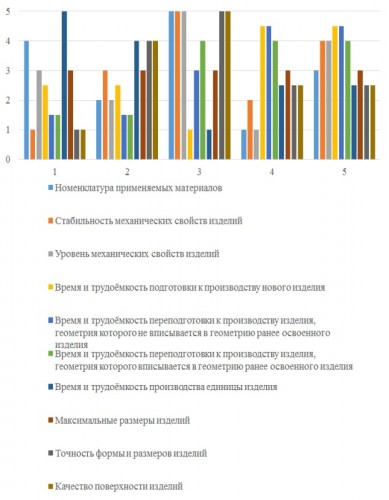
Рисунок 20. Сравнение современных аддитивных технологий
и традиционных технологий изготовления металлических деталей
Как видно из графика (рис. 20), аддитивные технологии сплавления (5) пока не достигли уровня традиционных технологий изготовления металлических деталей самолётов и вертолётов (3), а аддитивные технологии спекания (4) находятся приблизительно на одном уровне с литьевым производством (1).
В отдельных случаях решение в пользу той или иной технологии принимается даже если в краткосрочной перспективе прямой экономический эффект от неё будет отрицательным, но эта технология обеспечит уникальные характеристики самой продукции, а не производству. А современные аддитивные технологии сулят экономическую выгоду производству, но, к сожалению, пока не готовы доказать, что позволят сделать лучше продукты отрасли — самолёты и вертолёты [7].
Заключение
В России аддитивные технологии пока не достигли уровня традиционных технологий изготовления металлических деталей воздушных судов, хотя технологии сплавления и достаточно близки к нему.
Существующая в РФ нормативно-правовая база в области аддитивных технологий не способна регулировать их применение в отечественной авиационной отрасли. Отсутствие информации о механических свойствах синтезированных изделий, в первую очередь пределов выносливости, не позволяет ни применять аддитивные технологии в конструкции самолётов и вертолётов с точки зрения действующих на территории РФ норм лётной годности винтокрылых летательных аппаратов, ни даже приблизительно оценить перспективы применения аддитивных технологий в конструкции воздушных судов.
Опираясь на рассмотренный материал, можно прийти к следующему выводу: к сожалению, сегодня в отечественной авиационной отрасли применять аддитивные технологии представляется возможным только для изготовления макетов, прототипов и технологической оснастки.
Выходом в сложившейся ситуации может стать только государственная поддержка в виде федеральной целевой программы по созданию отечественных авиационных аддитивных технологий, предусматривающей с одной стороны, прикладные исследования технологий и материалов при участии разработчиков авиационной техники, с другой стороны — создание опытных образцов деталей авиационной техники на базе разработчиков аддитивных технологий. готовится «Комплексный план мероприятий по развитию и внедрению аддитивных технологий в Российской Федерации на период 2018–2025 гг».
План предусматривает:
- создание единой информационной среды;
- создание отечественных порошковых композиций нового поколения и отработка существующих режимов их синтеза;
- разработку системы нормативной документации для обеспечения внедрения аддитивных технологий на предприятиях государственных корпораций авиационной, ракетно-космической, судостроительной и атомной промышленности. Будем верить, что выполнение мероприятий Комплексного плана создаст фундамент для плодотворного совместного будущего отечественного авиастроения и отечественного аддитивного производства.
Безусловно, за аддитивными технологиями будущее, но не стоит воспринимать их как панацею, универсальный метод изготовления деталей. Инженеры понимают: каждый метод имеет свои ограничения в плане применимости – технологические, экономические, технические и прочие.
Сдерживающими факторами на данный момент являются высокие цены на материалы, оборудование, сложная и длительная процедура сертификации процесса производства на основе аддитивных технологий, недостаток опыта в работе с трудными сплавами титана и никеля на установках селективного лазерного плавления (СЛП). И наконец, отсутствие порошковых композиций, широко применяемых в нашей стране сплавов алюминия и магния, стали и прочее.
Я считаю, что все же, компромиссы в конструкции самолетов недопустимы, особенно если учитывать, что аппараты эксплуатируются по тридцать лет. Авиастроение хорошо знакомо с традиционными технологиями, при помощи которых создаются детали необходимой прочности. Что же касается АТ еще предстоит изучить все тонкости создания компонентов со сложной внутренней архитектурой. Ради этого придется провести массу испытаний на прочность в течение ближайших нескольких лет.
Но я уверен, что результатом таких исследований станет их широкое применение в авиационном дизайне, за ними будущее!!!
Источники информации
- https://ru.wikipedia.org/wiki/Аддитивные_технологии#Описание
- https://old.sk.ru/news/b/press/archive/2019/09/18/additivnye-tehnologii-_1320_-chto-eto-takoe-i-gde-primenyayutsya.aspx
- https://extxe.com/9626/vvedenie-i-istorija-additivnyh-tehnologij/
- https://extxe.com/3834/sushhnost-i-osobennosti-additivnyh-tehnologij/#Selective_Laser_Melting_SLM
- https://www.3dpulse.ru/news/zhurnal-additivnye-tehnologii/additivnye-tehnologii-dlya-aviakosmicheskoi-tehniki/
- https://www.pvsm.ru/3d-pechat/310942
- https://moluch.ru/archive/285/64365/
- https://avia.pro/blog/3d-pechat-v-aviacii-konstrukcionnye-plastiki-i-metally
- https://blog.iqb.ru/maks-2019/
- Тилинин, М. В. Аддитивные технологии в отечественном авиастроении: текущие позиции и направления развития / М. В. Тилинин, Б. М. Прибытков. — Текст: непосредственный // Молодой ученый. — 2019. — № 47 (285). — С. 133-138. — URL: https://moluch.ru/archive/285/64365/ (дата обращения: 03.12.2020).
- https://www.3dpulse.ru/news/zhurnal-additivnye-tehnologii/additivnye-tehnologii-dlya-aviakosmicheskoi-tehniki/
|