Мухаммат Масхутович Ульбашев, 15 лет, г. Нальчик, Кабардино-Балкарская Республика, Российская Федерация
Применение композиционных материалов в проектировании и строительстве летательных аппаратов с изменяемой геометрией и профилем крыла
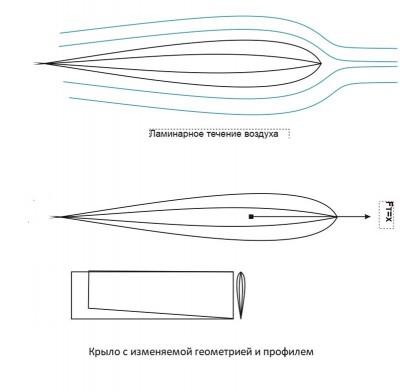
План:
Введение
Глава 1. Особенности полёта таймерных моделей
Глава 2. Использование композиционных материалов
2.1. Использование композиционных материалов в авиастроении
2.2. Способы формования КМ и целесообразность их применения
2.2.1. Матричный метод формования
2.2.2. Метод вакуумного формования
2.2.3. Вакуумная инфузия
2.2.4. Метод камерного формования
2.2.5. Пултрузия
Глава 3. Разработка и изготовление действующей модели с изменяемой геометрией крыла
3.1. Расчет количества армирующего материала и связующего
3.2. Контроль деталей в процессе обработки
3.3. Анализ качества структуры изделия радиационным методом
3.4. Изготовление модели с изменяемой геометрией крыла
3.5. Анализ эффективности применения КМ и результаты полетов
Заключение
Список литературы
Введение
Темпы внедрения композиционных материалов (КМ) в современное производство увеличиваются с каждым днём, используются не только в авиастроении, ракетостроении, но и в электротехнической и радиотехнической, оборонной промышленности, судостроении.
Использование КМ в двигателестроении позволяет снизить его массу, тем самым снизить расход топлива и увеличить маневренность летательного аппарата (ЛА). С другой стороны, применение КМ позволяет достичь увеличения полезной нагрузки.
Целью работы является создание крыла с изменяемой геометрией и профилем тем самым увеличить время полета спортивной таймерной авиамодели.
Для достижения цели были поставлены задачи:
- Исследовать свойства композиционных материалов и технологию их производства
- Выявить целесообразность того или иного вида формования в разных узлах конструкции летательных аппаратов.
- Разработать и изготовить конструкцию с изменяемой геометрией и профилем крыла.
- Изготовить действующие модели стандартов FAI: F1C разных видов и конструкций, провести сравнительный анализ эффективности применения композитных материалов и провести сравнительный анализ эффективности применения композитных материалов.
В данной работе описаны технологические процессы изготовления отдельных узлов и конструкций летательных аппаратов.
Объект исследования: технология изменяемой геометрии крыла и профиля в летательных аппаратах.
Предмет исследования: возможность увеличения продолжительности полета таймерной авиамодели.
Глава 1. Особенности полета таймерных моделей
Полет любой таймерной модели состоит из двух четко разграниченных этапов. Первый — моторный набор высоты. Главная задача - за ограниченное время при данной массе модели и объема двигателя поднять таймерную модель на возможно большую высоту и при этом разогнать модель до максимальной скорости. Второй этап полета — планирование. Задача удержать модель в воздухе максимальное время. Для этого используется эффект удлинения крыла и применением на крыле выраженных несущих профилей вогнуто-выпуклого типа. Указанные характеристики находятся в противоречии и требуют компромиссных конструктивных решений.
В крыле изменяемой геометрии на взлетных режимах «ушки», размах которых почти равен размаху центропланных частей, на петлях поворачиваются (перед стартом) вниз и ложатся на нижние поверхности центроплана. При постоянной хорде крыла в результате образуется несущая плоскость с динамичным, почти симметричным профилем, имеющая при этом в два раза уменьшенную площадь. После взлета «ушки» на переходном этапе раскрываются, и модель превращается в отличный планер с крылом высокого удлинения и с выраженным несущим профилем. Модель взлетает практически вертикально. После отсечки двигателя и исчерпывания кинетической энергии стабилизатор на еще не потерявшей вертикальной скорости модели на непродолжительное время переводится на положительный угол. Затем срабатывает механизм освобождения и раскрытия «ушек», и таймерная модель переходит на режим планирования.
Глава 2. Использование композиционных материалов
2.1. Использование композиционных материалов в авиастроении
Требования повышения лётно-технических характеристик сверхзвуковых самолётов, высокий уровень нагрузок конструкций в значительном диапазоне знакопеременных воздействующих напряжений потребовали разработки и использования самых современных высокоэффективных конструкционных материалов. Эту тенденцию развития за двадцатилетие наглядно показывают статистические данные, представленные диаграммой. [1]
Одним из ключевых направлений в ЛА является развитие технологий проектирования, производства и эксплуатации композитных конструкций самолётов и реализация на них ряда новых качеств.
Показателем усложнения конструкции ЛА служит дальнейшее повышение объёма применения полимерных композиционных материалов (ПКМ), что во многом определяет технический уровень изделий.
Преимущества КМ:
- высокая удельная прочность (прочность до 3500 МПа);
- высокая жесткость (модуль упругости 130…140 ГПа);
- высокая износостойкость;
- высокая усталостная прочность;
- снижение массы изделия;
- стойкость к вибро- и акустическим нагрузкам;
2.2. Способы формования КМ и целесообразность их применения
Выбор метода формообразования изделия из армированных композиционных материалов зависит от назначения изделия и габаритных размеров.
Операции по получению из композиционного материала изделия заданной формы и размеров, состоящая из следующих этапов: распределение на формообразующей поверхности исходных компонентов - армирующих материалов и связующего, приложение тепла и давления, сопровождающееся полимеризацией и отверждением материала в готовое изделие.
Первой стадией при формировании изделия из композиционного материала является нанесение на формообразующую поверхность (матрицу, оправку, форму и т.п.) антиадгезионного покрытия, в качестве которого используются: парафин, или мы используем пчелиный воск, растворенный бензином до однородной жидкой массы.
2.2.1. Матричный метод формования
В данной главе рассматривается технологический процесс изготовление оснастки (матрицы) воздушного винта и самого винта. В основе матрицы лежит дюралевый короб из 2х половин. Соответственно на одной половине матрицы создали внешнюю поверхность лопасти, а на второй половине внутреннюю. Установлены направляющие для соосного смыкания матрицы. По периметру формы просверлены отверстия с резьбой М6 для качественного прижимания ответных половинок матрицы во время парамелизации связующего.
Изготавливаемый воздушный винт мы делаем складывающийся, поэтому нам достаточно формировать 1 лопасть в матрице т.к. создать абсолютно идентичные формы очень сложно, а лопасти должны быть одинаковые.
После расчета количества используемого материала, необходимого для изготовления 1 лопасти, точится дюралевая втулка, которая в дальнейшем будет служить посадочным местом оси складывания винта. Современные двигатели требуют высоких прочностных характеристик вращаемых им лопастей, исходя из этого было решено вложить 4 слоя углеткани, но 2 из них под углом 45° относительно оси, которые будут работать на кручение, а 2 под 180°- работа на изгиб. (Рис.2)
2.2.2. Метод вакуумного формования
Вакуумное формование состоит из трех технологических операций: 1) получение заготовки; 2) обжатие этой заготовки с помощью резинового мешка под вакуумом; 3) отверждение.[5]
Давление, создаваемое при вакуумном формовании, составляет 0,5-0,8 кг/см2. Технологически операция вакуумного формования выполняется в следующем порядке (рис. 2). На форму позитивного или негативного типа, поверхности которой покрыты разделительным слоем смазки или пленки, наносится декоративный слой связующего. Поверх него выкладывается в соответствии с заданной схемой армированная ткань.
Для качественной пропитки и равномерной плотности структуры по всему сечению многократно повторяется нанесение слоя связующего и арматуры до получения заданной толщины стенки изделия.
Сверху на отформованную заготовку накладывается слой целлофана, что придает готовому изделию хороший внешний вид. (Рис.3.)
Вторым технологическим процессом является вакуумная опрессовка изделия (Рис.4.). Для этого полученная заготовка покрывается дренажным слоем для хорошего распределения вакуума, а затем резиновым чехлом, который герметизируется по краям и подсоединяется к шлангу вакуум-насоса. Сборка помещается в термокамеру, после чего под чехлом создается вакуум. Чем больше вакуум, тем выше его прочность и герметичность.
Третий технологический переход - отверждение отформованного изделия.
Достоинством вакуумного формования является его технологическая простота, несложность оснастки и оборудования.
Таким образом, было принято решение формовать кессоны для крыла модели самолета F1C, а также корочек для формирования всего крыла.
Следующий метод формования, который был исследован это вакуумная инфузия.
2.2.3. Вакуумная инфузия
Характеризуется тем, что подача связующего осуществляется через подающую трубку за счет создания вакуума в оснастке. Таким методом была сформирована хвостовая балка фюжеляжа (Рис.5.) [3]
2.2.4. Метод камерного формования
Этот метод основан на использовании жесткой формы негативного типа (пресс-камеры) и упругого (надувного) пуансона (рис.4). Внешняя поверхность стеклопластикового изделия оформляется поверхностью жесткой формы, а внутренняя - упругим резиновым чехлом. Такой вид формования подходит для формирования носовой части фюзеляжа модели F1C, так как имеет формы, характерные для использования именно этого метода формования (Рис. 6.).
Предварительно отформованное изделие помещаем в жесткую пресс-камерную форму, стенки которой способны выдержать большое внутреннее давление. Внутрь заготовки вводится резиновый чехол, шарик, после чего в него подается сжатый воздух, который создает рабочее давление упругого формования от 1,5 до 5 кг/см2. Однако воздух, оставшийся между чехлом и формуемой массой полуфабриката изделия, может скапливаться в застойных зонах и при формовании испортить структуру материала. Это не позволяет получить качественной поверхности, плотности, герметичности и отрицательно сказывается на механической прочности. Поэтому для повышения качества пресс-камерного формования рекомендуется применять вакуумный отсос воздуха из-под резинового чехла.
Таким образом, технологическая структура операции пресс-камерного формования выглядит так: предварительное формование полуфабриката, вакуумирование (при необходимости), отверждение.
2.2.5. Пултрузия
Пултрузия - экономичный метод производства прямых композитных изделий с постоянной площадью поперечного сечения. [4]
Пултрузионная установка (Рис.7) включает в себя систему подачи волокна, полимерную ванну, нагретую фильеру (пресс-форму), синхронизированную тянущую машину и отрезную машину.
В качестве полимеров обычно используют полиэфирные, эпоксидные смолы. В последнее время используют специальные «пултрузионные» смолы и отвердители, оптимизированные для пултрузионного процесса, это повысило скорость процесса до 4…6 метров в минуту (первые пултрузионные установки имели скорость протяжки около 1 м/мин.) Наиболее часто используемыми в пултрузии волокнами являются стекло и углеволокно. В работе было решено использовать лонжероны крыла, выполненные таким способом, так как они имеют один профиль на всем удлинении крыла.
Глава 3. Использование современного оборудования
Современное программное обеспечение позволяет передать только что созданную трёхмерную геометрию детали непосредственно на станок с числовым управлением.
Современные станки с ЧПУ, во-первых, имеют практически прямую связь с персональными компьютерами. Во-вторых, повышается количество степеней свободы. Если старые станки могли обеспечить не более 3,4 степеней свободы, то сегодня 12 степеней свободы - норма. В-третьих, повышается точность станков, так как современные станки в автоматическом режиме проводят измерение и коррекцию траектории инструмента относительно заготовки в зависимости от величины изнашивания инструмента. Все это в свою очередь позволяет снизить трудоемкость, повысить ресурс, повысить точность изготовления.
Следовательно, дальнейшее развитие производства вызывает необходимость в реализации новых путей совершенствования технологии.
3.1. Расчет количества армирующего материала и связующего
Расчет количества армирующего материала, производим используя схему раскроя и приложения программы КОМПАС-3D V8 Plus+.
Расчет количества связующего был рассчитан относительно массы армирующего материала каждого изделия.
Схема раскроя
Производим расчёт:
- требуемой площади (площадь накладки), учитывая количество слоев ткани, необходимой для укладки;
- массы связующего, необходимого для пропитки углеткани. Концентрация связующего для пропитки армирующих наполнителей составляет 51%.
- Определяем угол укладки волокон каждой детали:
Центроплан
|
45º 180º 45 º
|
Хвостовая балка
|
180 º 90 º
|
Кессоны
|
45 º
|
Лонжероны и задняя кромка
|
180 º180 º
|
Воздушный винт
|
45 º 180 º 45 º
|
- Определяем количество материала толщиной 0.27мм
Центроплан
|
3,85
|
Хвостовая балка
|
9,37
|
Кессоны
|
20,8
|
Лонжероны и задняя кромка
|
4,7
|
Воздушный винт
|
2,25
|
3.2. Контроль деталей в процессе обработки
Если при извлечении панели из оснастки размеры детали не соответствуют заданным, то применяем механическую обработку: подрезаем торцы, удаляем припуски на механическую обработку, чтобы достичь нужных размеров.[2]
Контроль деталей в процессе обработки оснастки, заготовок, сравнение с 3D-моделями, инспекция поверхностей, калибровка, контроль матриц, быстрое прототипирование будущих изделий, обратный инжиниринг, позволяет совершать 3D гравер-сканер RolandMD-40 (Рис.8.)
С помощью RolandMD-40 на рабочую зону устанавливается объект измерения, подключается компьютер и с помощью программного обеспечения калибруют щуп, которым производятся измерения. После этого прибор готов к работе. На эту процедуру уходит от 15 до 20 минут, после чего у нас имеется ЗD проект сканируемой поверхности. Контроль производится точечным контактным способом, т.е. для снятия какой-либо точки, необходимо зафиксировать щуп на изделии и снять показания.
3.3. Анализ качества структуры изделия, радиационным методом
Работа основана на радиационном методе контроля с использованием излучения рентгеновских аппаратов и радиоактивных источников. Компьютерный рентген-аппарат позволил оценить качество заполнения связующего в композитной лопасти.
3.4. Изготовление модели с изменяемой геометрией крыла
Большая часть элементов модели изготовлена из углепластика, соответствующим для их геометрии способом. Сборка конструкций и узлов производится на стапелях для исключения перекосов и круток конструкции.
Требования повышения лётно-технических характеристик, высокий уровень нагрузок потребовали разработки и использования самых современных высокоэффективных конструкционных материалов.
Последовательность операции по получению из композиционного материала изделия заданной формы и размеров состоит из 2 этапов. Чтобы получить деталь необходимо распределить армирующие материалы на формообразующей поверхности в зоне высокой температуры и давления.
Первой стадией при формировании изделия из композиционного материала является нанесение на формообразующую поверхность (матрицу, оправку, форму и т.п.) антиадгезионного покрытия, в качестве которого используются: парафин или воск. Нервюры для каждого крыла и стабилизатора изготавливаются из бальзы 1,5 мм. Далее подготавливаем трубчатые лонжероны для установки в них пружины для раскрытия.
3.5. Анализ эффективности применения КМ и результаты полетов
Анализ эффективности применения КМ в конструкции планера модели выявил лучшие прочностные и аэродинамические характеристики, исключили такое понятие как флаттер при увеличении размаха крыла, возможность разрыва лопастей центробежной силой, вибрации хвостовой балки во время взлета модели, улучшили результаты полетов что отражено в таблице 1. Тестовые испытания показали увеличение высоты подъёма и времени планирования.
- Рассмотрены особенности полета таймерных моделей.
- Построена модель с изменяемой геометрией крыла.
- Проведен анализ полета моделей.
Таблица результатов полетов таймерных моделей.
Модель
|
Время работы двигателя
|
Объем двигателя
|
Высота взлета
|
Время планирования
|
1
|
3.85 сек
|
2,5 см3
|
67м
|
250 сек
|
1
|
3.85 сек
|
2,5 см3
|
65м
|
275 сек
|
1
|
3.85 сек
|
2,5 см3
|
69м
|
230 сек
|
2
|
3.85 сек
|
2,5 см3
|
132м
|
620 сек
|
2
|
3.85 сек
|
2,5 см3
|
141м
|
512 сек
|
2
|
3.85сек
|
2,5 см3
|
138м
|
598 сек
|
Заключение
Обзор технической литературы, выявил особенности полета и направление совершенствования таймерных моделей. Прежде всего необходимо уменьшить лобовое сопротивление при взлётном режиме и адаптировать конструкцию в режиме планирования.
Построена модель с изменяемой геометрией крыла, которая позволяет уменьшить лобовое сопротивление крыла при подъеме.
В процессе постройки модели возникла необходимость проектирования петель и замков для возможности раскрытия крыла.
Проведен обзор технологий формования композиционных материалов, применяемых в строительстве БПЛА.
Исследованы свойства композиционных материалов, технологии их производства. Для каждой детали используется определенный вид формования в зависимости от ее геометрии.
Выявлена целесообразность различных видов формования в разных узлах конструкции летательных аппаратов.
Предварительные запуски моделей подтвердили преимущество изменяемой геометрии и профиля крыла, которые заключаются в том, что уменьшение лобового сопротивления происходит за счет гашения турбулентности, что ведет к увеличению набора высоты на взлетном режиме.
Список литературы
- Технология производства изделий из КМ: Учеб. пособие, Вамболь А.А., Шевцова М.А.-Х.: Национальный аэрокосмический университет «Харьковский авиационный институт», 2005, 28 с.
- Кривенда С.П. Оформоение технической документации на изделия из КМ: Учеб. пособие- Х.: Национальный аэрокосмический университет «Харьковский авиационный институт», 2004, 50 с.
- А.В. Гайдачук, М.А. Сидоренкова Учебное пособие «Технология производства изделий из полимерных композиционных материалов», «Харьковский авиационный институт» 1998г., 98 с.
- Учебное пособие «Технология производства летательных аппаратов из композиционных материалов», Киев, 1995г., 374с.
- Ивановская О.В., Шевцова М.А. технология производства изделий из полимерных композиционный материалов- Х.: Национальный аэрокосмический университет «Харьковский авиационный институт», 2005, 98 с.